Datum & Datum Reference Frame (DRF)
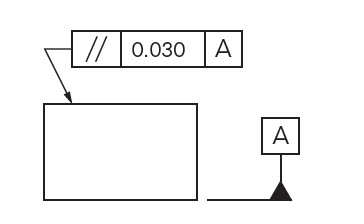
The primary is the first feature contacted (minimum contact at 3 points), the secondary feature is the second feature contacted (minimum contact at 2 points), and the tertiary is the third feature contacted (minimum contact at 1 point). Contacting the three (3) datum features simultaneously establishes the three (3) mutually perpendicular datum planes or the datum reference frame.
If the part has a circular feature that is identifi ed as the primary datum feature then as discussed later a datum axis is obtained which allows two (2) mutually perpendicular planes to intersect the axis which will be the primary and secondary datum planes.
Another feature is needed (tertiary) to be contacted in order orientate (fi x the two planes that intersect the datum axis) and to establish the datum reference frame. Datum features have to be specifi ed in an order of precedence to properly position a part on the Datum Reference Frame. The desired order of precedence is obtained by entering the appropriate datum feature letter from left to right in the Feature Control Frame (FCF) (see Section 5 for explanation for FCF).
The first letter is the primary datum, the second letter is the secondary datum, and the third letter is the tertiary datum. The letter identifies the datum feature that is to be contacted however the letter in the FCF is the datum plane or axis of the datum simulators.
Datum Reference Frame (DRF)
The DRF is probably the most important concept of GD&T. In order to manufacture and/or inspect a part to a drawing , the three (3) plane concept is necessary. Three (3) mutually perpendicular (exactly 90° to each other) and perfect planes need to be created to measure from. In GD&T this is called Datum Reference Frame whereas in mathematics it is the Cartesian coordinate system invented by Rene Descartes in France (1596-1650).
Often one would express this concept as the need to establish the X,Y, and Z coordinates. The DRF is created by so-called Datum Simulators which are the manufacturing, processing, and inspection equipment such as surface plate, a collet, a three jaw chuck, a gage pin, etc. The DRF simulators provide the origin of dimensional relationships.
They contact the features (named Datum Features) which of course are not perfect hence measurements from simulators (which are nearly perfect) provides accurate values and they stabilize the part so that when the manufacturer inspects the part and the customer inspects the part they both get the same answer. Also if the part is contacted during the initial manufacturing setup in the same manner as when it is inspected, a “layout” for assuring machining stock is not required. The final result (assuming the processing equipment is suitable for the tolerancing specified) will be positive.